|
|
|
|
|
|
|
|
|
|
|
|
 |
|
|
 |
|
|
|
|
|
|
|
|
|
Riccardo, what makes the KR Audio facility unique compared to other present-day tube manufacturers? |
|
|
Our manufacturing facility is different from most other tube plants in that they use automated mass manufacture while we do it the old-fashioned way. We exclusively craft our products by hand like the great artisans at Rolls Royce. Our tubes undergo many stages during the manufacturing process, from the initial tooling to the formation of the chemical coating, from the mechanical assembly to the application of a high vacuum and the kind of QC a high-volume plant cannot perform.
To give you a clearer idea of the quality and time that go into each KR Audio tube: Each tube receives a hand-blown glass envelope and its own internal matriculation number. A normal 300B designed in the 1930s had 28 internal components; the KR 300B has 128. While we can produce 500 tubes per month, mass-producation facilities using robotic carousels can run off that same amount in one day. Any reader interested to learn more is welcome to write or visit us in Prague to observe the many steps involved in making a truly hand-crafted tube from scratch.
|
|
|
 |
|
|
 |
|
|
What sets KR Audio tubes apart from others? |
|
|
The most unique characteristic of any KR tube is its exceptionally long life. We give it that with the enormous care put into it. I view it as my duty to make producst that lasts. The Leak amplifiers I bought in 1959 are still working beautifully. Any manufacturer of consumer electronics products should feel obligated to create an "appliance" that works without problems, lasts a long time, gives wonderful results and can be passed down to the next generation as something to cherish. It should not fall onto the pile of obsolete junk where so many of today's unloved pieces of electronics end up, discarded to make space for whatever new is promoted as better. |
|
|
 |
|
|
 |
|
|
Tell us about the R&D process that leads up to an utterly novel tube for which there are no precedents - like your super high-power triodes. |
|
|
 |
The development of a completely new product is both easy and hard. Since there are no precedents, you suffer no mental limitations that could stop you by whispering how it couldn't be done. I'm grateful for my experience as a young man, when I began to work in a large manufacturing company that had started making radios in 1923.
They produced tubes for their own televisions and continued to produce hybrids later on. But I realized that my own company could incorporate higher standards of quality, as well as offer valuable assistance to designers wanting to improve their tube amplifier performance.
Yes, the trial and error process, cutting down trees to clear a path during the prototype phase so to speak, is always challenging. It was the same for our specialists working on our latest novelty, the T-100 triode. We were the first to incorporate a Titanium plate during the development of the KR 52BX. This has now evolved into its substitute, the KR 842. All our tubes are high-powered triodes specifically designed for audio use only. It is my fervent hope that transmitter tubes will eventually remain where they were intended to be used - in radio transmission instead of audio playback devices. |
|
|
 |
|
|
You specialize in triodes though the KR KT-88 you produce is technically a tetrode. Explain this focus and why you're not interested in pentodes. |
|
|
As an old-timer with tubes, I'm interested in all tube technology. However, pentodes cannot be successfully manufactured using our process. We were cooperating with another line production facility here in Prague, to build the KR KT-88. But our high QC standards could not be sustained by Tesla. The quality we received for our design was unacceptably low, unworthy of the KR brand name and trademark. With great disappointment, we had to suspend our work with the Tesla people. |
|
|
 |
|
|
 |
|
|
|
|
|
|
|
|
|
Explain the sonic 'flavors' of the different tubes you make. If output power were of no concern -- because ancillary speakers were high-sensitivity -- which one is your personal favorite? |
|
|
You will probably smile when I say this, but all the tubes our engineers and specialists have developed with me have become very much like my own children. Each child (tube) has had an easy or difficult birth; a happy or less successful career when compared against its brothers or sisters. Being that I love music in general, their distinct sonic flavors are loved by me equally. I was personaly reponsible for their conception and upbringing and they're all dear to me and close to my heart.
Over my years in the audio industry, I've learned how listening is so far more subjective than eye sight, and how many people have what audiologists refer to as "aural" memory. In a certain sense, these are colors that specific musical performances imprint on a person's nervous system to make them recognize sounds as they remember them.
For instance, even though musicians are supposed to enjoy perfect pitch and recall of the same, the monitoring process of the brain centers where this sound imprint is stored is stimulated to recall only when one hears these sounds again.
The greatest sins in this regard are commited today by the use of massive PA speaker systems that accompany rock stars and magnify the distortions of small amplifiying tubes in guitar amplifiers. Because musicians deliberately overdrive tubes that already suffer poor mechanical sealing, faulty vacuums and original defects from the supplying manufacturers using outdated automated carousel techniques, the sound of these popular groups is changing from performance to performance. This causes subliminal confusion with the listeners who no longer possess a clear imprint of what things should really sound like.
|
|
|
 |
|
|
 |
|
|
Draw a picture for us of life in Prague if one loved music - about the local music scene, concerts, audiophiles, stores, clubs and so forth. |
|
|
Here I must confess that my age does not permit me to participate as fully as I might wish, in the marvellous musical life that Prague has to offer its residents, its visitors and the Czech public in general.
After the withdrawal of the Soviet troops, everything that was once forbidden in music (Jazz, Dixieland, Rock, Country, Western, any other form of experimental or what was then called "degenerate" music") sprang back to life. Formerly secret Jazz clubs could once again operate openly. Cellars became nightclubs. People could indulge whatever musical inclinations struck their fancy.
|
|
|
|
|
|
|
|
 |
|
|
|
|
|
|
|
|
 |
|
|
|
|
|
Envelope from Prague containing Dr. Kron's final papers
|
|
|
|
Even though my mother's father was Czech (and I believe my interest and gift in mechanical things was transmitted via these maternal genes) I was surprised to find a very good basic music education in our Czech school system. Most of my engineers play instruments. They more easily understand the natural sound reproduction. They simply refer to their aural memories of concertizing.
But let me return to the Prague music scene. On any given afternoon, there are always concerts going on, in the churches, in the Municipal hall, in the various formal concert halls.
There even is a cowboy radio station, right alongside my favorite classical FM frequencies that have won awards for their wonderful programming. The discoteques are many as the Czeck people have access to the archives of the Bonton recording studios that made a number of excellent masters during the Communist regime.
The Prague Philharmonic Orchestra, if not on tour, is a thing of beauty that absolutely should not be missed if you're in town and they're in residence. And while I can't guarantee musical Nirvana if someone came to Prague, your choices are very varied. There are even collector's shops for antique records, but thus far I haven't yet come across any audiophile clubs. Perhaps someone reading this might prove us wrong?
|
|
 |
|
How about your ampifier designs? |
|
|
|
 |
|
Well, that's intimately tied to our proprietary KR tube technology. Our engineers differ from other amplifer designers in that when a tube is finalized, the amplifier is developed around it. With most other designers, the basic circuitry exists a priori. The output power tube is added later and has to conform to limitations in the basic pre-existing architecture.
Our designs are developed from the ground up with only one goal in mind - to get optimum results from a particular tube we designed ourselves. We are consistently testing and sourcing better and better parts and materials to fine-tune this process. One example is the application of SIMAX hard glass to all our tube envelopes. It dissipates heat faster than regular glass and thus enhances tube life and performance.
I have developed both solid-state and what the lay perosn would call hybrid amplifier designs. For example, our double Kronzilla that won "Best Sound of Show" in Germany this year, uses a solid-state driver stage for maximum voltage swing to drive our colossal KR 1610 triode.
You may rightfully wonder why a tube manufacturer has categorically declined to work with low-level preamplifying tubes in his designs. And I would reply that no small-signal tube on the market today meets our specs. Our solid-state driver stages outperform any tubes we've tested.
I should be convinced of this statement as I've been asked to produce a small-signal tube. When I did, it was considered cost-prohibitive to use in real-world designs and thus abandonded.
The development of our solid-state driver circuits in response to these two situations has led me and my engineering team to believe that the use of transistor drivers with high-power triode outputs combines the best of both worlds and allows us to address the inconsistencies between recorded and live music.
When played back over one of our KR-designed amplifiers, these discrepancies becomes very small. Music again sounds like what our aural memory trained on live events tells us it should.
|
|
|
|
|
 |
|
|
|
|
|
|
|
|
 |
|
|
|
|
|
 |
|
|
|
|
|
To e-mail Dr. Eunice Kron,
click on her card.
|
|
|
|
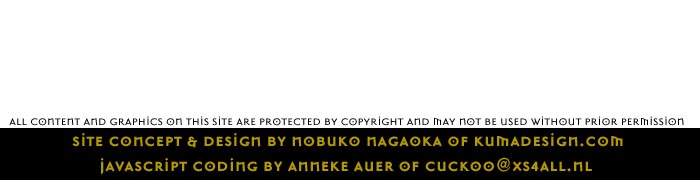 |
|