 |
|
|
Where the D26 sets a standard for high-frequency reproduction and state-of-the-art dome driver design, the D50 carries the same philosophy down into the crucial midband covering 880Hz to 4kHz. Featuring the same computer-designed deep catenary profile and anodized aluminium-alloy diaphragm, the D50 maintains pistonic behaviour more than two octaves beyond its operating band, with a first breakup frequency of 20kHz. The comparison with my own K1 now stops. The G1’s low mid and bass drivers require different solutions.
|
|
C125S
|
Designed specially as the low midrange Giya unit, the C125S sports the same diaphragm assembly as the 4 x C125 units of the K1 but features a magnet system which takes advantage of the smaller excursion requirements for a driver which only works above 220Hz. A shorter magnetic gap with reduced coil clearance and solid copper pole sleeve increase the flux focus for a 3dB efficiency increase over the C125 of the Oval line. The C125S loads like the D50 and D26 into a fibre-filled rear tube that’s exponentially tapered to fully absorb the rear output. Isolation between magnet system, horn and enclosure comes from high-compliance elastomeric seals between each element. In this way the reactive forces of the motor system are contained within the driver without direct mechanical excitation of any external modes.
As were all other Vivid Audio diaphragms, the C125 cone was optimized using computer-aided finite element analysis to delay the first break-up mode. In this particular case, Dickie’s research led to a solution with an unusually shaped central dome that’s not so much dust cap as integral structural element. The
C125S chassis are made from pressure-cast aluminium with a unique construction in which twelve supporting struts have an unusually narrow aspect ratio and align to present minimal airflow obstruction. Their 3mm wide legs represent just 10% of the cone area to effectively render them acoustically invisible. The compact rare-earth radial magnet assembly complements this chassis with its small frontal area.
A further function of the chassis is to act as heat sink for the motor assembly. The cooler the voice coil, the smaller its power compression as drive levels increase. By having a large number of chassis struts which sit relatively deep next to their point of attachment to the magnet, the chassis turns into a highly efficient finned heat sink of nearly thrice the conventional radiating area.
|
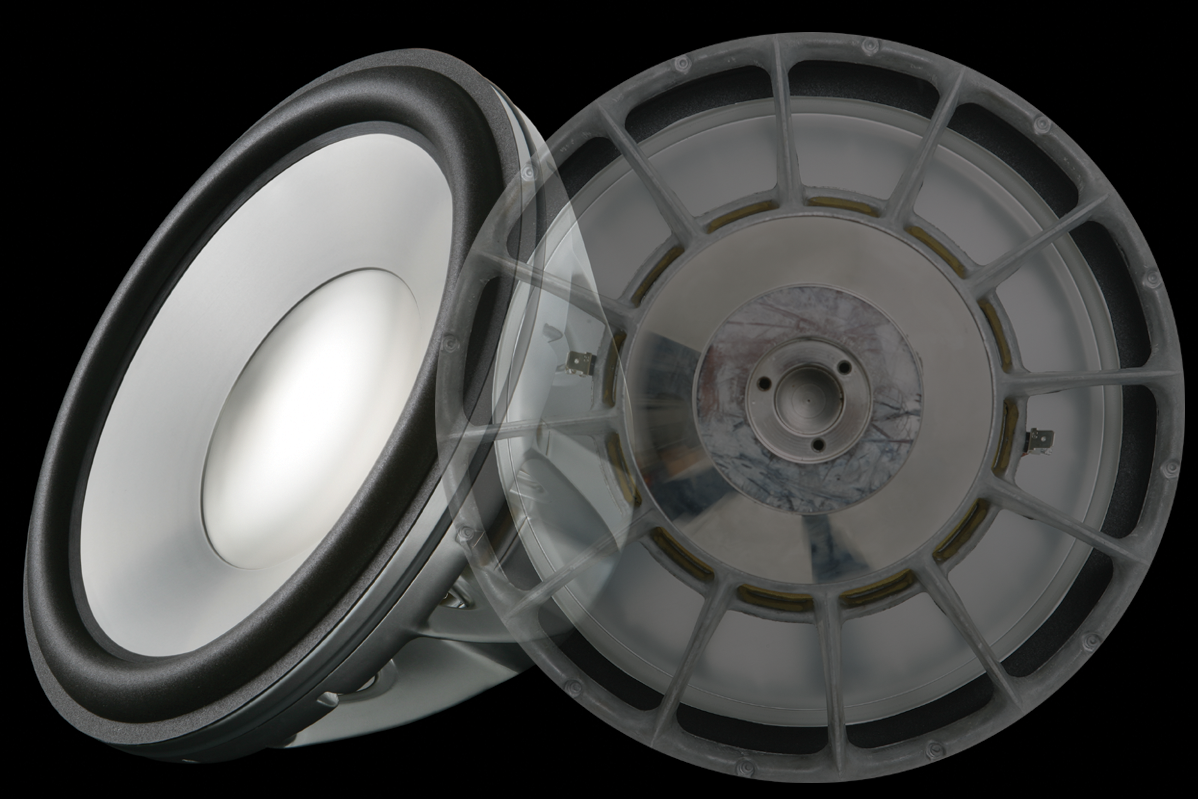 |
C225
|
The Giya flagship then gets its own woofers called C225. These share many family traits with the C125 including the highly aligned radial struts. Laurence Dickie designed these woofers for a 4-way speaker with drastic requirements of out-of-band performance. Thanks to its generous 225mm diameter, the all aluminium-alloy diaphragm extends pistonic operations to beyond 2kHz! With such a comfortable margin between crossover and first break-up mode, it ensures the most important purity level in the pass-band.
|
|
|
|
Like the C125, the C225 includes 12 highly aligned radial struts for the smallest obstruction to the rear wave.
Just as you wouldn’t buy a sport car with an underpowered engine, the C225 features a specially adapted motor. It includes a 12mm long coil in a 35mm gap for 23mm of linear excursion. The overall mechanical reach of 54mm ensures the capacity to move massive amounts of air. This impressive requirement is served by a 75mm diameter aluminium ribbon voice coil to reduce operating temps for minimized power compression. Despite such exceptional gap length, a flux of nearly 1 Tesla remains along its full length via the use of radial magnet tech. This creates an extraordinary level of force from the input current which, combined with a very low moving mass of 50g, is able to provide the fastest most articulate bass.
The horizontally opposed woofers work as a unified system in a force-cancelling compliant mount. Dickie’s approach to the basic Newtonian law of motion where every action produces an equal and opposite reaction is based on rigidly coupling his woofer magnets. As long as both drivers receive identical power, their opposing forces will cancel mechanically to prevent any transmission into the enclosure. Both woofers are driven with identical signals below 100Hz. Above that a differential force begins to appear which is accounted for with a pair of elastomeric O-rings under each driver rim.
|
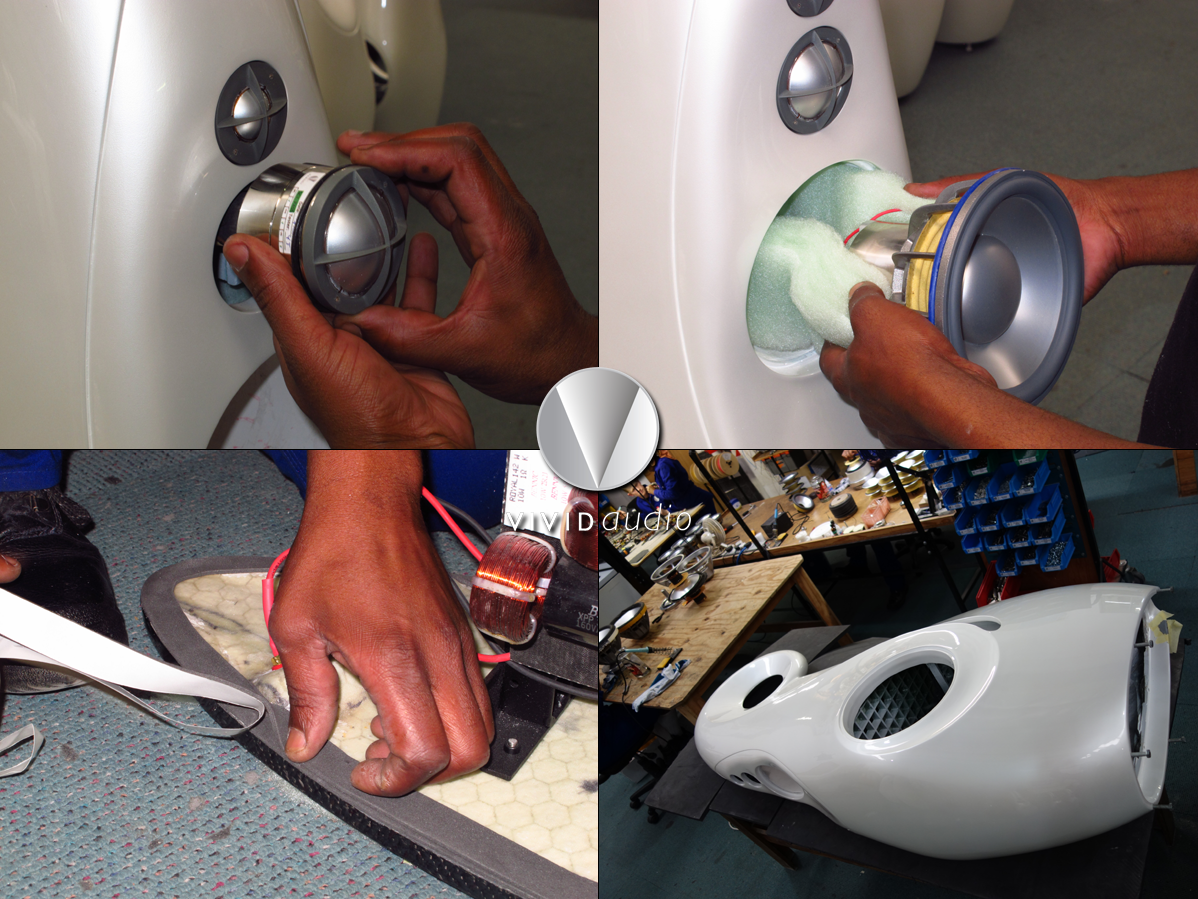 |
The Giya crossover is something which really impresses. It’s rather hard to get a precise notion of its sheer size just looking at photos but believe me, it’s really a huge structure divided in two separate parts, one dedicated to the woofers, the other to the mid/high drivers. As a true four-way design, the G1’s filter is far from simple. Designer Laurence Dickie employs a series/parallel square approach to maintain linear impedance across the band and match the drivers’ acoustic roll-off. Symmetrical polar performance is obtained with 4th-order 24dB/octave Linkwitz-Riley slopes. This gives ideal phase and summation response and a symmetrical dispersion pattern. Dickie claims that the computer-based Giya crossovers creates complete sub-system responses which easily compete with what might be achieved by active filtering. All Vivid Audio crossovers are built in-house and not contracted out which is not a given today. The two woofers cross to the midbass driver at 220Hz, the midbass hands over to the midrange dome at 880Hz and the dome tweeter operates from 3.5kHz to 29kHz.
|
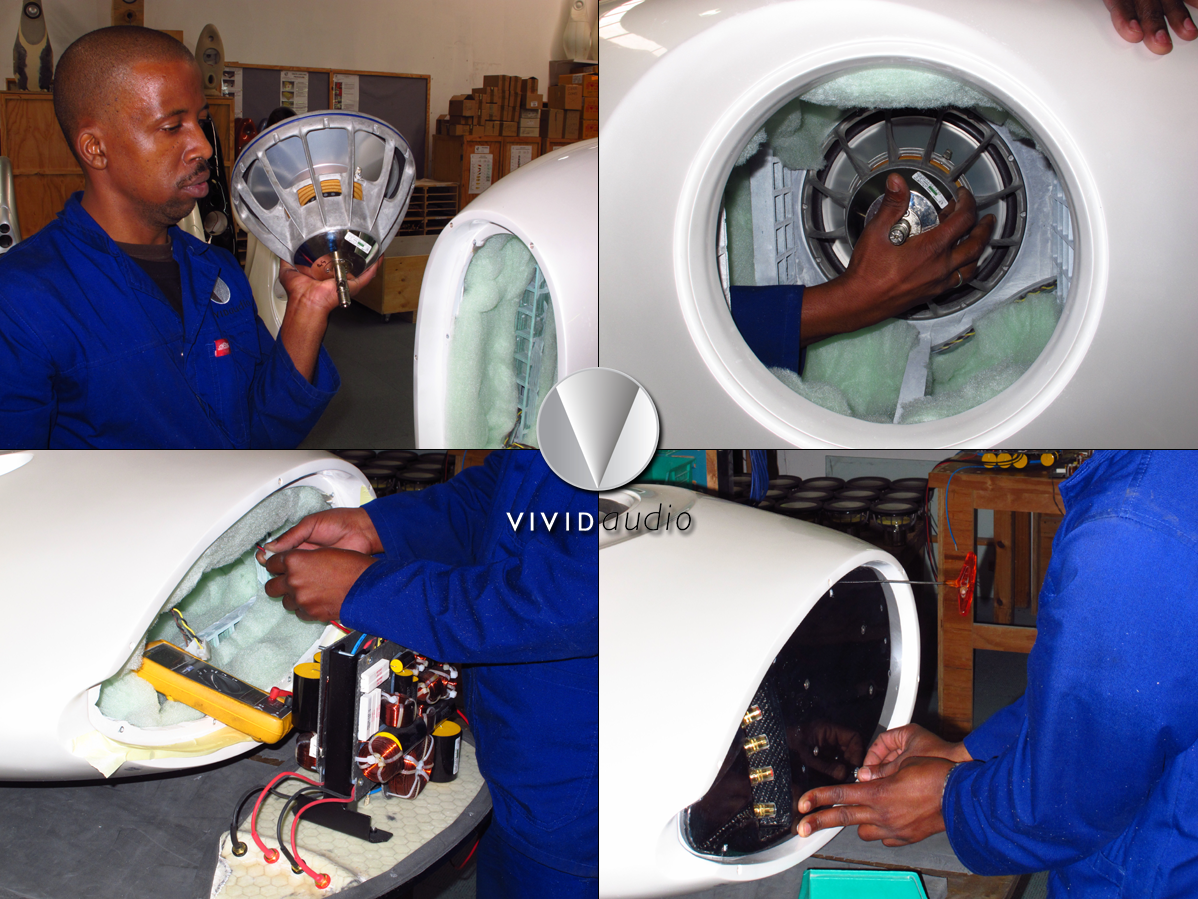 |
Delivery. Two big crates shipped from Durban to Paris left me no time to forget the imposing Lawrence Audio crates I had received in June. This time I had to face even larger boxes of nearly 270kg! Unlike the
Lawrence Audio Double Bass containers, each wooden box came equipped with two handles and two rollers. Two guys could thus move these monsters without trolley assist. I had to open both crates to find the two wooden rails which get affixed to each crate. Now the speakers which arrive bolted to a wooden board using their bottom spike threads could be slid out easily. Protective foam guaranteed complete inertia of the speaker inside its sarcophagus during transit and a certificate insured that all quality control checks were passed successfully.
|
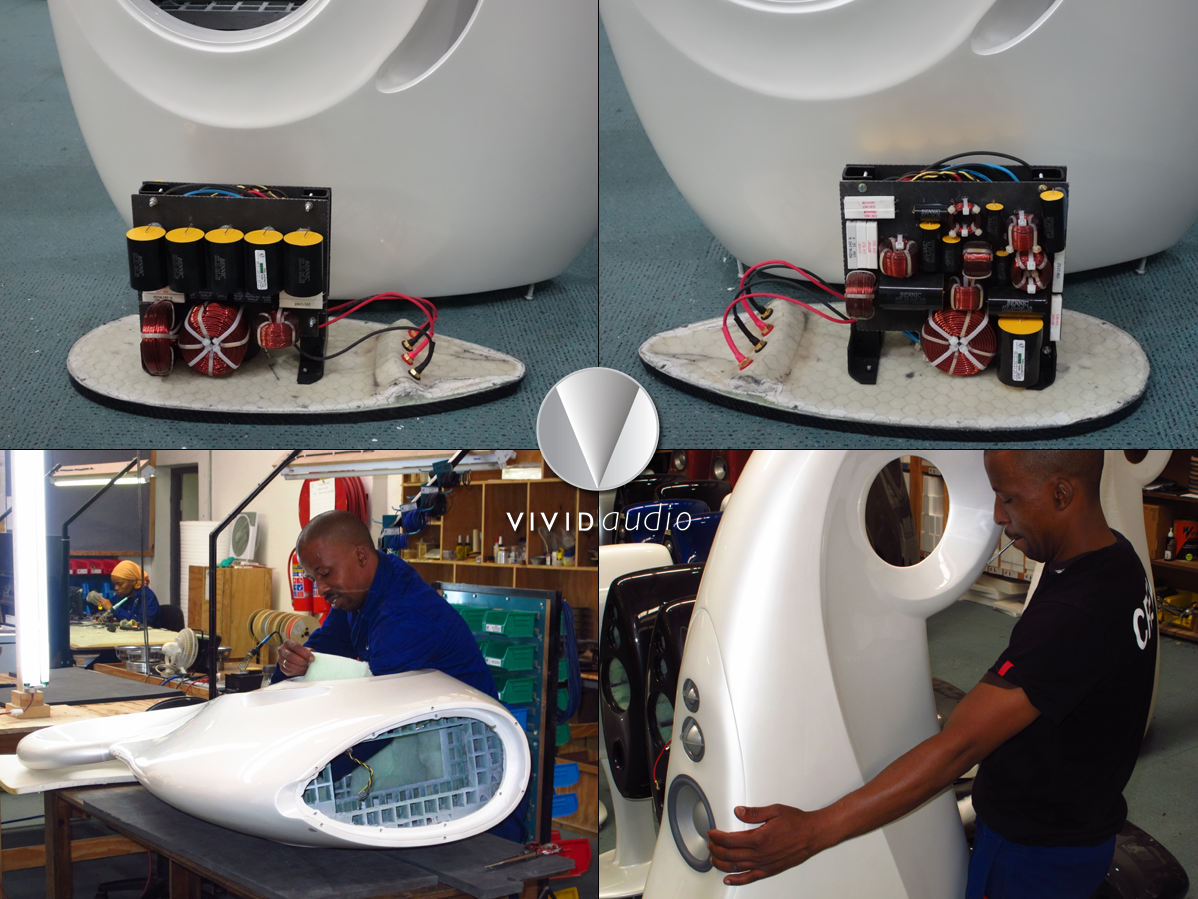 |
I had no choice but to open the crates in my garage. Their size and weight didn’t allow direct transportation into my upstairs listening room. A good surprise was that thee speaker weight outside the box was down to 70kg each. It was now possible to move them upstairs. But remove the wooden board first since the screw holes are in a thin wall. The speakers arrive with a set of spikes and feet. The black rubber feet can be directly screwed into the bottom threads or be reversed to act as floor protectors for the spikes. The rubber feet were a nice option to slide the speakers around on the pavement. The sole issue with them is their limited height. It makes for crammed space to connect the floor-facing terminals to speaker cable. On that count my K1 weren’t that user-friendly either but the Giya becomes even more problematic. Wiring them up requires almost two people, one to pull the top of the speaker toward him whilst the other connects the now exposed binding posts on the belly. Payback is a superbly clean appearance. It's perhaps the only element where the speaker’s shape doesn’t really serve a function.
|
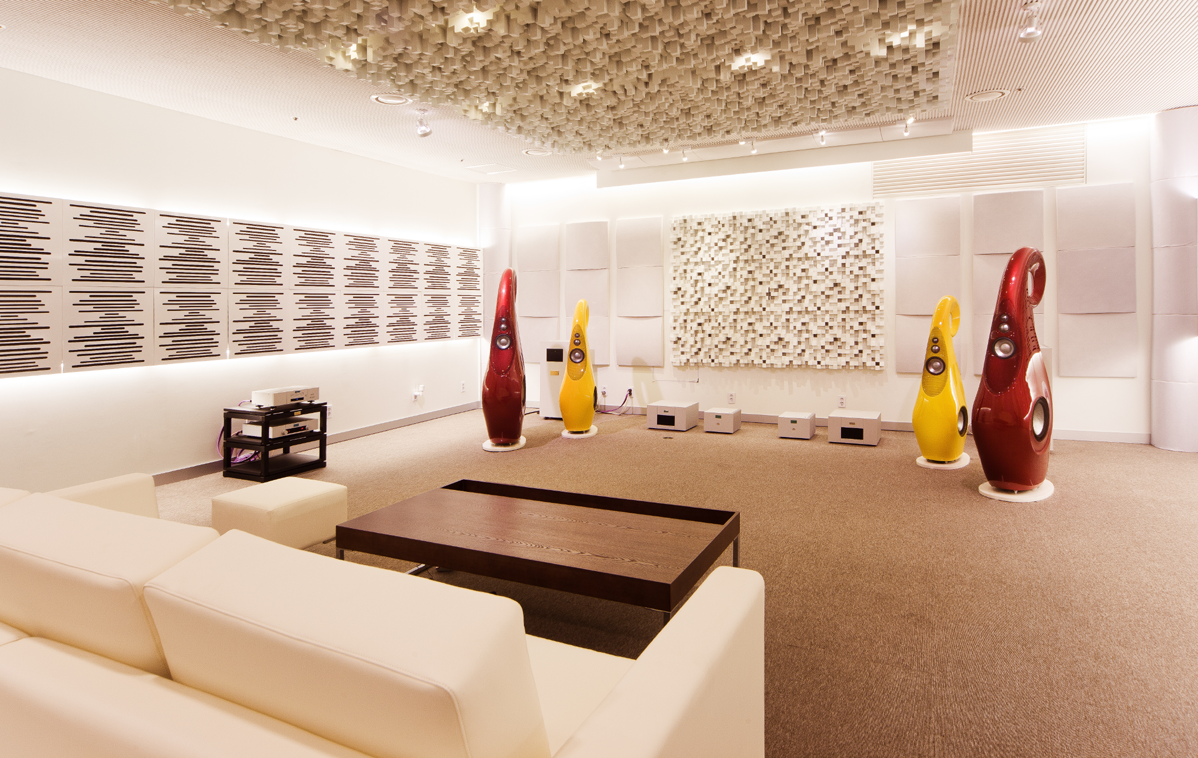 |
Vivid/Goldmund showroom in Korea.
|
Once installed in my listening room, Philip Guttentag, CEO of Vivid Audio, flew to Paris for a few days to assist me with correct setup. As my loaners were brand new, I was told that it would take almost 300 hours before I’d face the speakers’ true capabilities. So I planned on a lot of listening before starting to put pen to paper.
|
|
 |
|
|
|
|