SideBar 1: More about Dynamic Power Delivery Supply (DPDS) and other technical refinements.
Traditional DC power supplies are specified into a constant current draw with a resistive load. Except for class A amplifiers (and Class AB at low power) however, the load is not linear. The power supply is therefore specified for the maximum current drawn. The Genesis DPDS on the other hand was designed to deliver current into a non-linear, dynamic musical load with the objective of providing a sense of power with finesse. The expected result according to Genesis is that the Reference Amplifier should have the dynamics, extension and drive of high-power transistor amplifiers without their muscle-bound sound; and the elegance, emotion and tonal colors of flea-powered single-ended triode amplifiers without being weak or flaccid.
Specifically from the GR360 manual: The origin of the DPDS derives from the principles of tube amplifier design some of the qualities of tube amplifiers had as much to do with power supply design as the choice of tubes over transistors. Because of the high voltages involved, tube amplifiers use relatively small capacitors and chokes to produce smooth DC power. Transistor amps use cheaper/larger electrolytic capacitors to do much the same job. From this we discover a very simple fact, namely that smaller capacitors usually sound better. This is not mere speculation. There is good science to predict that the high frequency performance of large capacitors will be poor. There are lots of very small solid-state amplifiers with excellent sound. They all have tiny power supplies and the smaller the power supply, the 'faster' they sound. On the other hand, very large power amplifiers with huge capacitors or even large banks of smaller capacitors in their power supplies tend to sound slow and 'muscle bound'. The DPDS in the simplest illustration used the frequency distribution of music and Fletcher Munson curves to predict the required power delivery to play back music. Then it uses a class D amplifier module as a 'perfect music-driven faucet' to deliver current to the connected loudspeakers. This is the issue of speed vs power. The sprinter is not able to sustain the delivery of power for very long but the marathon runner is not able to deliver very quick bursts of speed. The DPDS is like a relay team with sprinters, medium distance and long distance runners in the team. Thus it is able to deliver high power as well as very quick bursts of speed. Such a 'relay team' is what gives the Genesis Reference Amplifier the excellent microdynamics, tonal contrasts and timbral textures of low-lowered amplifiers yet is able to deliver huge dynamics and sustained deep bass of muscle amps.
The optional Maximum Dynamic Headroom Reservoir extends this ability down to loudspeaker impedances of 1 ohm and below, by extending the relay team and adding proprietary resonance control circuitry to ensure that the 'baton handover' from one team member to the next is handled as smoothly as possible. This results in increased dynamics from having more current available into lower impedance loads and better microdynamics. One listener described it as "having cream in your coffee instead of non-fat soy".
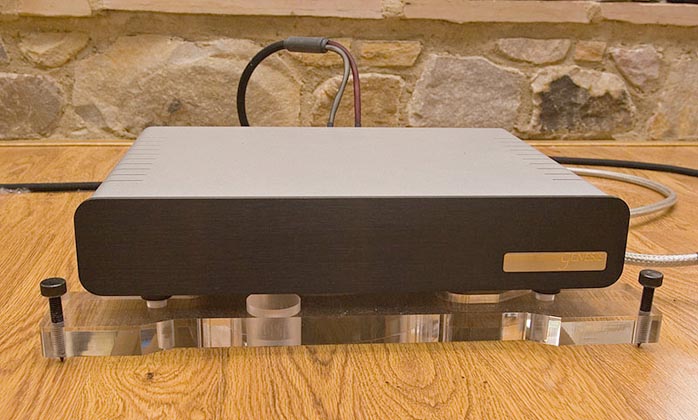
About vibration control
With Genesis putting a lot of emphasis on reducing noise and distortion from the power supply coming into the amplifier, it would make no sense if the amplifier itself created vibration. Hence one additional feature worth mentioning is the outboard power transformer. According to Gary Koh, there is no way to completely eliminate hum and vibration from the transformer. Neither should you want to try. This is because even for the best-built transformer, the incoming 50Hz or 60Hz in the coils will shake the steel in the transformer core. In addition, if the incoming power is not a perfect sinusoidal waveform, the transformer will rattle and buzz even more. [My 1.8KVA 80 lbs balanced isolation Plitron transformer to step down 240V to 120V is so quiet, you can't tell whether it's powered on. I'm not certain I buy the argument that it isn't possible or desirable to have perfectly quiet big transformers - Ed.]
From the GR360 manual again: A single switch-mode power supply in the electrical circuit will cause asymmetric compression of the power waveform. Moreover, noise-generating devices such as light dimmers, electric curling irons, microwave ovens etc. can also cause the transformer to vibrate at those noise frequencies. Capacitive coupling between the primary and secondary windings of the transformer will cause that noise to also result in high frequency noise bleeding through from the input to the output. A phenomenon that we noted in the design of the transformer is that when the coils are wound so that the transformer does not emit any audible hum, the transformer will vibrate and heat up even more. It is intuitive that the incoming sine wave needs to be dissipated in some way in the form of sound, heat or vibration.
With the transformer moved outside of the chassis, the Genesis Reference Amplifier has a much quieter environment in which to operate. To further reduce the vibration/resonance within the chassis, the signal and power circuits are further isolated from each other. The signal circuits are softly hung using a neoprene blanket from the top cover of the chassis, while the power circuits are stiffly mounted on the bottom using plastic standoffs. This is because of the different susceptibility of the two different circuits to different frequencies of vibration and resonance.
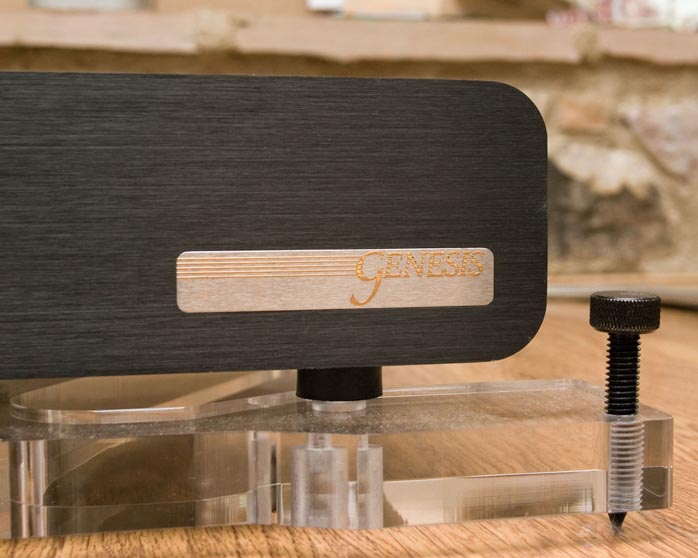
Acoustic Suspension System
A dedicated suspension system completes the resonance and vibration control design of the Genesis Reference Amplifier. Designed like the suspension system of a race car, the acoustic suspension is made of a solid acrylic frame, neoprene shock absorbers and steel spikes. It isolates the amplifier from floor- or structure-borne vibrations while allowing any vibration in the amplifier chassis to be sunk to ground. The function of the steel spike is as a low-impedance point to transfer all frequencies to ground. This is possible because the contact at the point of the spike is smaller than a ½ wavelength of the frequencies to be transmitted. Using a steel cup under the spike will defeat this function as this will only allow frequencies that have a ½ wavelength larger than the diameter of the steel cup, far larger than the point of the spike. Hence if the amplifier is to be placed on a hardwood floor and you do not want to mar the floor, use a copper penny under each spike. The weight of the amplifier on the spike will deform the penny and create a small indentation. The other side of the indentation will form a little nipple to couple to the hardwood floor.
I will vouch for the excellence of this setup. As delivered originally, one of the spikes was not fitting in its dedicated threaded hole (a problem of conversion between metric and US measurements) and I had to wait for a few days for a replacement spike. Meanwhile the GR360 rested, as is typical in my system, on three SoundQuest Isol-pads. As the spike arrived, I put it in place and let the amplifier rest directly on the floor coupled only through the spikes. Surprisingly, focus tightened and bass extended deeper, confirming the quality of the solution implemented by Genesis. My recommendation is therefore to use the GR360 as designed and not bother with amplifier platforms unless you are ready to spend significantly more than the price of four Isolpads in hopes of a hypothetic improvement.
|
|